HAMM- 100 YEARS OF INNOVATION & EXPERIENCE
It was in 1911 when Hamm developed the first road compaction equipment with a diesel engine – since then our innovative team has been designing trend-setting machinery. Today, HAMM is the world‘s major producer of asphalt rollers and soil compactors.
HAMM is famous worldwide for powerful and user-friendly compaction machines for a wide variety of jobs associated with road construction and earth works. Moreover, Hamm rollers are convincing because of their ergonomic and innovative design. HAMM has been awarded a total of 20 design prizes for all its innovations.
Hamm 3516 compactor is one of the typical products in Hamm Series 3000, ranging from mid-range compactors and weighing from 10 tons to 25 tons. With over 30 different product models, including smooth drum type, padfoot drum typecombination drum type. Because of the perfect combination of factors such as: strong operation, user-friendliness, fast, optimal compacting ability but extremely reasonable price. And most of all, besides bringing many economic benefits to the business, soil compactor 3516 has many other values such as fuel saving, construction and environmental protection.
We offer a broad range of services in all areas of road construction and refurbishment. With passion and dedication our highly motivated team ensures your success at the construction site.
Market-leading products and top service with tried and tested quality standards give you the confidence you need in your fiercely competitive environment. The Wirtgen Group’s successful brands of long standing will safely keep you on the road to success.
TECHNICAL DATA
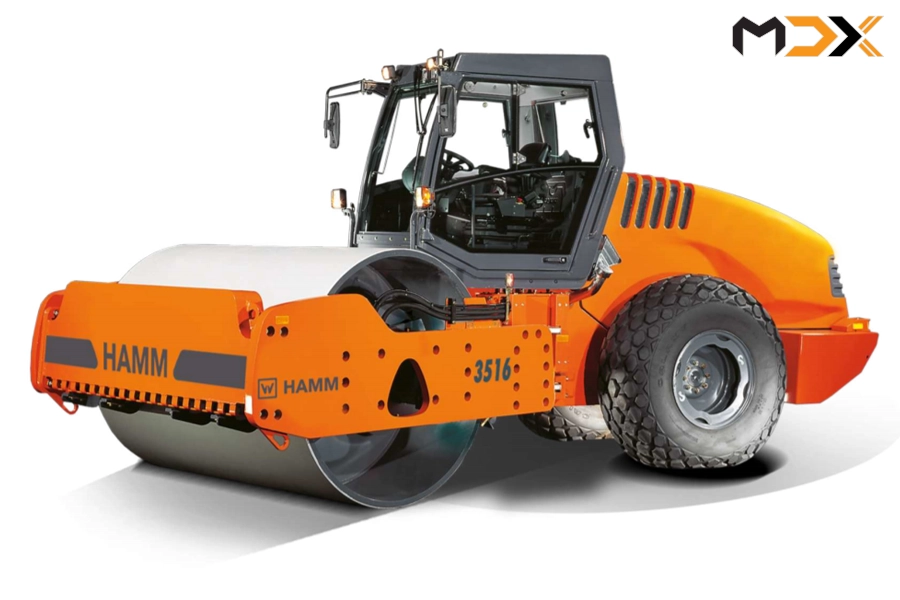 |
|
Unit |
3516 |
WEIGHTS |
Operating weight with cab |
kg |
15 755 |
Operating weight with ROPS |
kg |
15 535 |
Operating weight, max. |
kg |
18 810 |
Axle load, front / rear |
kg |
9 305 / 6450 |
Static linear load, front |
kg/cm |
43,5 |
French classific., data/class |
|
59,96 / VM4 |
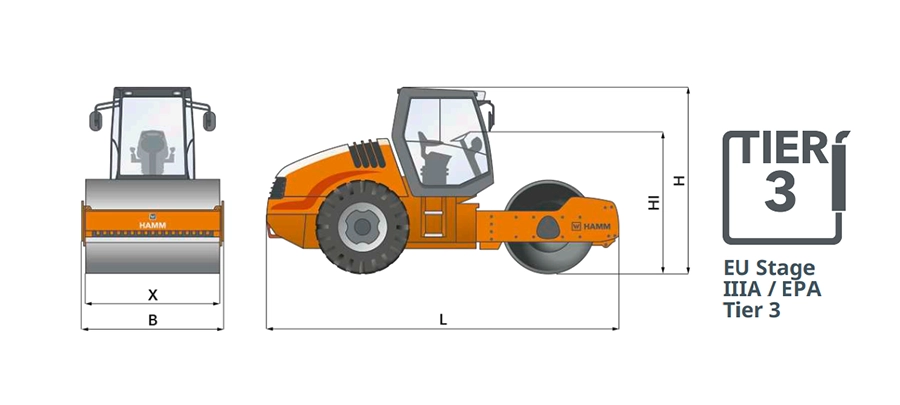 |
MACHINE DIMENSIONS |
Total length (L) |
mm |
6 075 |
Total height with cab (H) |
mm |
3 020 |
Height, loading, min. (HI) |
mm |
2 290 |
Wheelbase |
mm |
3 090 |
Total width with cab (B) |
mm |
2 270 |
Ground clearance, center |
mm |
375 |
Turning radius, inside |
mm |
4 360 |
Angle of driving slope, front / rear |
° |
31 / 27 |
DRUM DIMENSIONS |
Drum width, front (X) |
mm |
2 140 |
Drum diameter, front |
mm |
1 504 |
Drum thickness, front |
mm |
30 |
Drum type, front |
|
smooth |
WHEEL DIMENSIONS |
Size of tires, rear |
|
AW 23.1-26 12 PR |
DIESEL ENGINE |
Manufacturer |
|
DEUTZ |
Type |
|
TCD 2012 L06 2V |
Number of cylinders |
|
6 |
Power rat. ISO 14396 |
kW/PS/rpm |
155,0 / 210,8 / 2 300 |
Power rating SAE J1349 |
kW/PS/rpm |
155,0 / 207,7 / 2 300 |
Emission standard |
|
EU Stage IIIA / EPA Tier 3 |
DRIVE |
Speed, working gear |
km/h |
0 - 4,4 / 0 - 5,9 / 0 - 6,9 |
Speed, transportation gear |
km/h |
0 - 11,3 |
Climbing ability, vibration on/off |
% |
47 / 52 |
VIBRATION |
Vibration frequency, front, I/II |
Hz |
30 / 40 |
Amplitude, front, I/II |
mm |
1,91/0,90 |
Centrifugal force, front, I/II |
kN |
256/215 |
STEERING |
Oscillation angle +/- |
° |
10 |
Steering, type |
|
Articulated steering |
TANK CAPACITY / FILL CAPACITY |
Fuel tank, capacity |
L |
290 |
SOUND LEVEL |
Acoustic power LW(A), sticker |
db(A) |
105 |
Acoustic power LW(A), measured |
db(A) |
103 |
EQUIPMENTS
Note: standard or optional equipment depends on the standard of each country. Please contact us for the answer.
STANDARD: 2 armrests, 3-point articulation, Adjustable scraper, Dashboard with displays, indicator lights and switches, Automatic traction control and anti-slip control, Battery isolation switch, Control console with steering column adjustment, Operator’s platform with entry from both sides, Speed preselect, Hydrostatic steering, Vibration-isolated operator’s platform, Stepless hydrostatic allwheel drive, Handrails on the operator’s platform, Dozer blade.
OPTIONAL: ROPS, rigid, Auxiliary heater, Radio, Protective roof, Padfoot shells, Version with additional fuel prefilter, HAMM Compaction Meter (HCM), Speedometer, Frequency display, vibration, Back-up alarm (reversing), Automatic vibration system, Working lights, Rotating beacon, Protective grille for lighting package, Hose protection.
HIGHLIGHTS
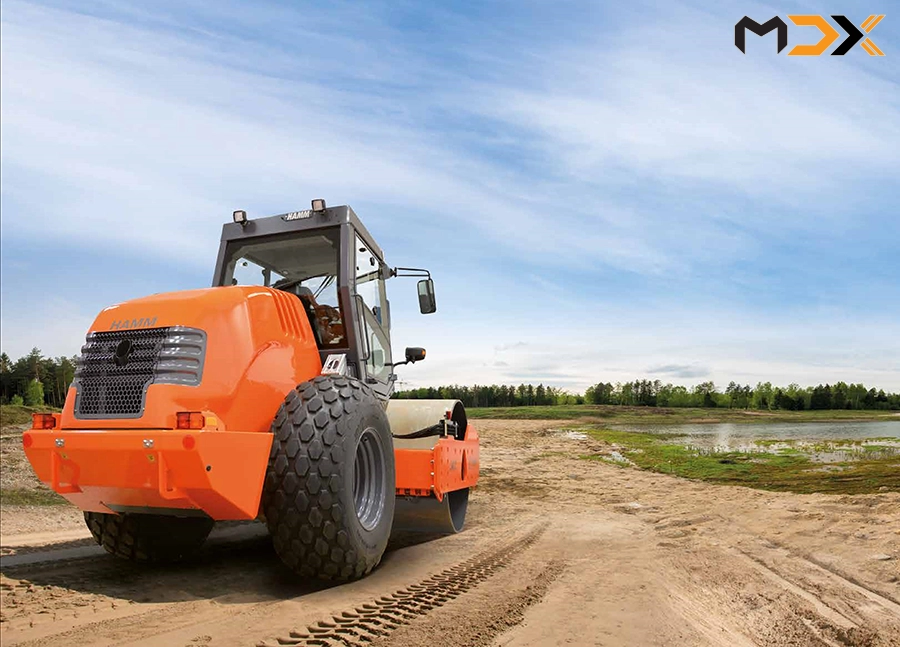
ROPS cabin with perfect all-round visibility. Outstanding view of the machine and surrounding construction site from the driver’s seat. 12 V socket, storage compartments, drinks holder and stacker as standard. Air conditioning and/or auxiliary heater available as optional extras.
Option. ROPS available for all machines, with or without protective roof according to preference.
Option. Camera with display on the operator’s platform for easier monitoring of the area behind the machine.
Comfortable driver’s seat, individually adjustable and swivelling. Adjustable armrests. Height-adjustable backrest. Steering column individually adjustable.
Bright working lights, main headlights with LED or halogen lamps, depending on the modelOutstanding off-road mobility, absorbs shocks. Unrivalled driving stability, high resistance to tipping and top-class directional stability make for safe manoeuvring even on rough terrain.
Drive control with one or two joysticks, depending on the model. If equipped with Hammtronic, preselection of maximum speed and automatic support when reversing are included.
Robust, water-cooled 4 or 6-cylinder engines. Comply with the requirements of EU Stage II / EPA Tier 2 or EU Stage IIIA / EPA Tier 3, depending on the model version. Optional fuel pre-filter available.
Option. Electronic machine management system for monitoring of all engine and vehicle functions. Automatic adjustment of traction and vibration/oscillation drives and engine speed to the prevailing operating conditions.
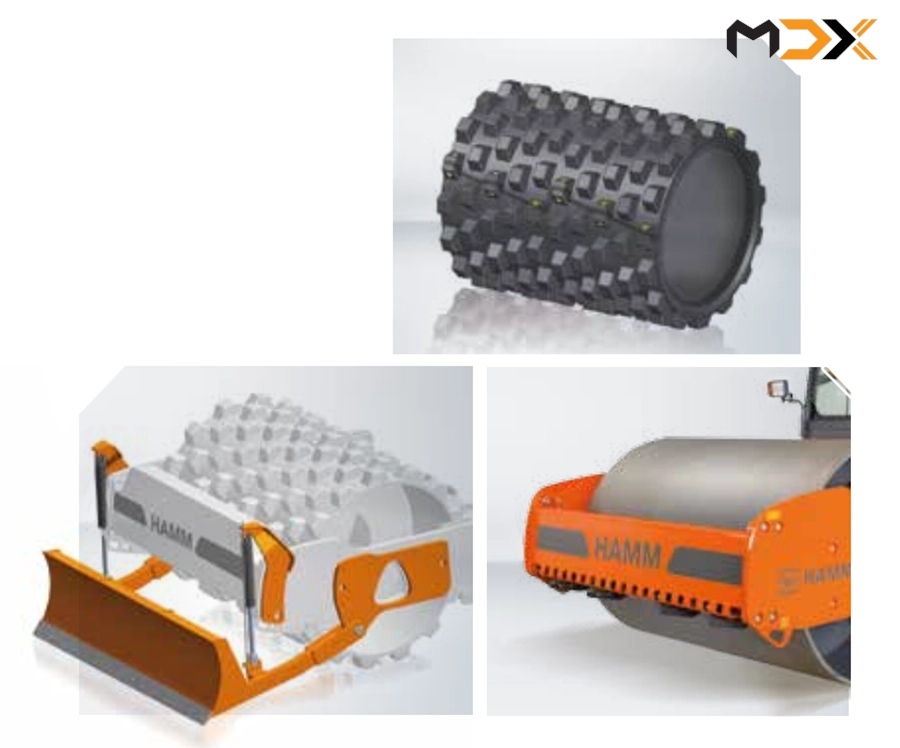
Available with smooth drum or padfoot drum. Three-section split padfoot segments also available. Some models also available with VIO drum (vibration or oscillation).
Option. Available for selected models with smooth or padfoot drums.
Option. Compaction meter, measures the rigidity of the ground in order to monitor compaction.
Option. System for comprehensive compaction control and documentation.
Come as standard with universal tread profile for machines with smooth drum or with tractor profile for machines with padfoot drum. Earth Mover tyres (EM profile) available as an option.
HAMM 3416 - Mastering every slope

Ingenious power train concept provides a climbing ability in excess of 60%
Hamm compactor 3516 is true classics for earth work because they combine modern design with proven engineering. They put their capabilities to the test day in, day out, in every corner of the world. One of their outstanding features is their climbing ability. Depending on the model and configuration, they can scale inclines of 60% or more, compacting extremely efficiently as they go.
- On the models equipped with Hammtronic, the anti-slip control and continuously variable hydraulic motors ensure optimum traction force at all times.
- On the compactors equipped with Hammtronic, the load-dependent speed control protects the engine and reduces fuel consumption.
- The rear axle with self-locking differential prevents wheelspin.
- The 3-point articulation ensures uniform weight distribution between the front and rear sections and thus outstanding traction even in rough terrain.
Perfect overview
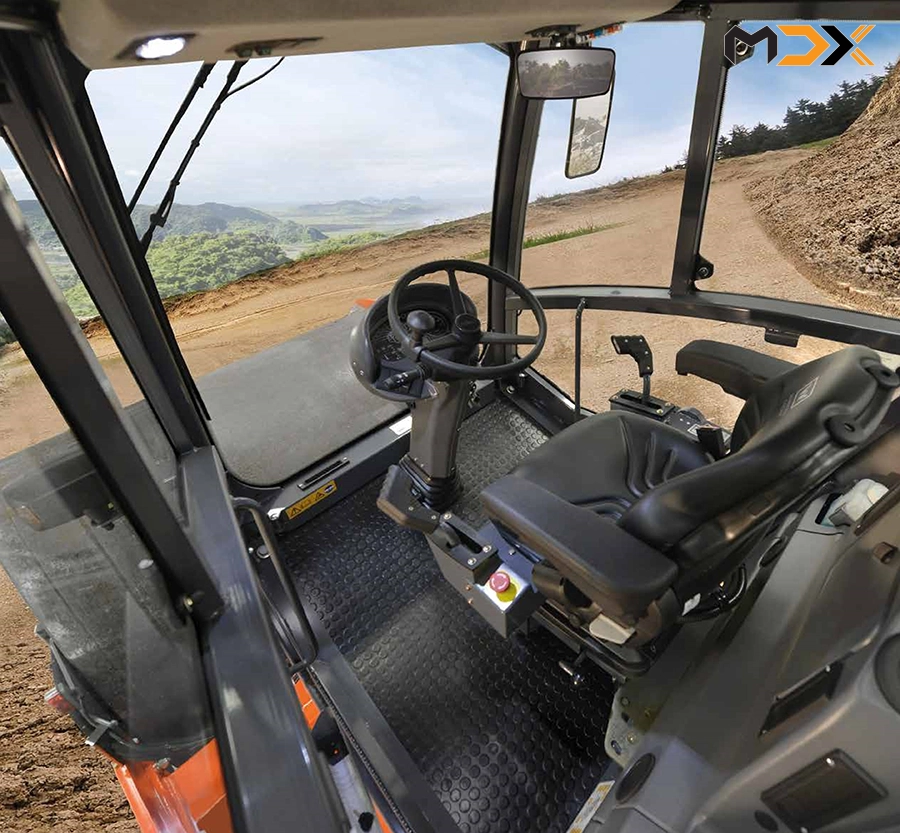
Hamm compactor 3516 offers ergonomically optimised workspaces as standard. They allow roller drivers to work with total concentration for many hours at a stretch.
Ergonomically optimised and comfortable
Soil compactor 3516 offers operators plenty of space because every model has a large cabin or operator’s platform, accessible from either side. Another practical and comfortable feature is the spring-mounted, height-adjustable driver’s seat. It can be turned, moved to either side, and also moved forwards and backwards on most models. The rake of the steering column with the dashboard is also continuously adjustable to match. Here, every driver is sure to find his ideal working position.
Outstanding visibility
In addition, there is superb all-round visibility because the cabin and doors are fully glazed. This gives the driver a clear view of the drum at all times. The tyres and the space behind the roller are also fully visible because the engine hood has a slimline, sloping shape and the exhaust pipe is positioned so as not to interfere with the all-round view.
- The cabin can be supplied with or without air conditioning.
- Unobstructed view of the drum
- Continuously adjustable steering column.
- Comfortable driver’s seat, individually adjustable for height and weight.
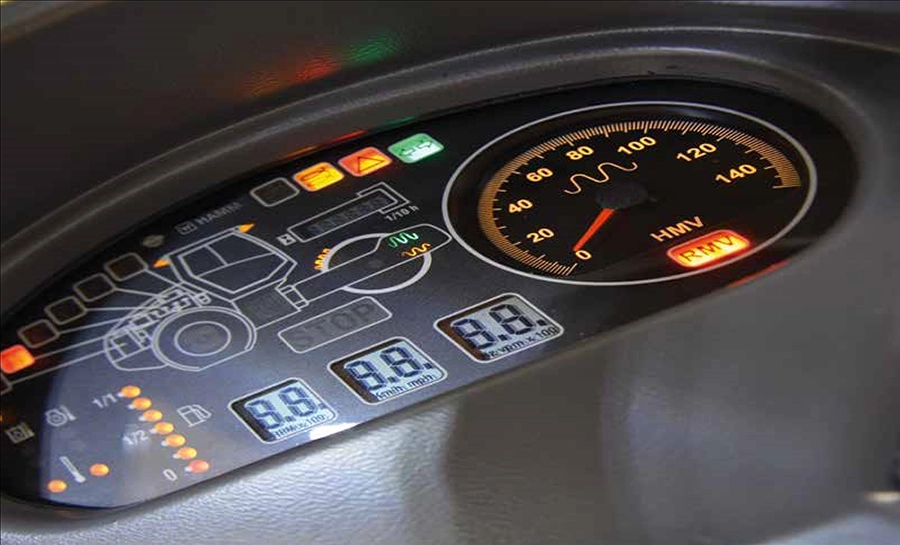
Operation? It couldn’t be easier!
Display of the HMV value on the dashboard
Clear cockpit overview
In terms of operation, drivers of Hamm compactors 3516 have it really easy: everything is clearly laid-out and self-explanatory. Drive control is via one or two drive levers, depending on the model. The activation switch for the vibration is also located on the drive lever, so that the two most frequently used functions can be controlled with one hand.
The dashboard is notable for its unambiguous, internationally understandable marking and labelling. Here, HAMM has dispensed with language, using clear symbols instead. As a result, these compactors can be operated entirely without language skills and yet always with comprehensive information on the current operating status of the machine – an important prerequisite for highquality ground compaction.
Durable engine technology - For a long machine life
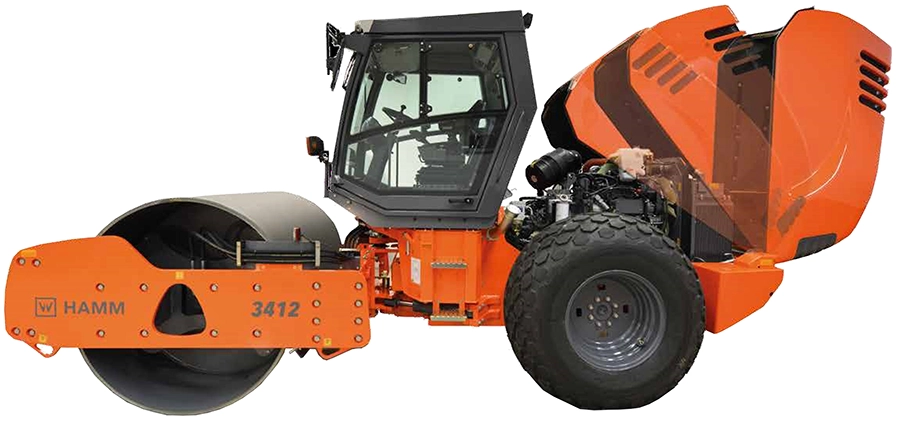
HAMM has also provided for efficient maintenance of the rollers because all maintenance points are located on the same side of the machine.
Efficient and economical
Robust 4 or 6-cylinder Deutz diesel engines in the Series 3000 compactors provide ample power with which to drive all components. At the same time, they have adequate reserves for efficient compaction, even under extreme conditions. They comply with the EU Stage II / EPA Tier 2 or EU Stage IIIA / EPA Tier 3 requirements – that means low exhaust emissions and low fuel consumption.
Intelligent airflow enables the rollers to be operated even in high ambient temperatures. A supplementary fuel filter can also be installed. It eliminates excess water from the diesel fuel, ensuring reliable operation
Quickly done: daily maintenance
The few maintenance tasks on Hamm compactors 3516 are quickly done because the wellilluminated engine compartment is very low, making it readily accessible for the workshop technicians. The engine hood provides another benefit: thanks to the cleverly selected position of the pivot point, it can be opened wide, even in restricted headroom situations. Moreover, all maintenance points and the battery are easily accessible on one side of the machine.
Solutions for value retention
HAMM offers various modules for intelligent maintenance. The most important solutions:
WIDIAG
WIDIAG enables WIRTGEN GROUP service technicians to read out the roller’s data log on the construction site. In the event of a fault, this speeds up the diagnosis because WIDIAG supplies valuable pointers to the source of the trouble.
WIDOS
WIDOS covers the complete spare parts catalogue, all instructions, hydraulic, electrical and hose system plans, machine data and documentation, safety instructions, component pictures and service documentation in numerous languages – on paper or CD.
WITOS
WITOS is the WIRTGEN GROUP’s intelligent telematics system for efficient fleet and service management. A SIM card allows the machine data to be transmitted automatically to the WIRTGEN GROUP service professionals. They determine the optimum time for the necessary maintenance work and deal with the upcoming tasks. In this way, the residual value, availability and performance of the HAMM rollers will be kept at a high level for a long time.
Flexible earth work professionals - Universally employable in earth work
With well over 30 different models, Hamm compactor 3516 covers the entire spectrum of medium and heavyweight compactors. It also includes various smooth and padfoot drums as well as different compaction systems. This makes the Series 3000 compactors universally employable – for example in roadbed compaction, earth work or building construction, building embankments and slopes and for compaction during cold recycling or soil stabilisation.
- Working lights with LED or halogen spotlights.
- The compactors of Series 3000 are available with ROPS, cabin, protective roof or completely open.
- Available with vibrating or VIO drum (operates with vibration or oscillation), depending on the model.
TECHNOLOGIES
3-POINT ARTICULATTION
3-point articulation is different to conventional joints due to its geometric arrangement and connection of the three individual joints and one additional connecting link between the two conventional upper joints. This allows optimum steering, excellent driving safety and maximum driving comfort.
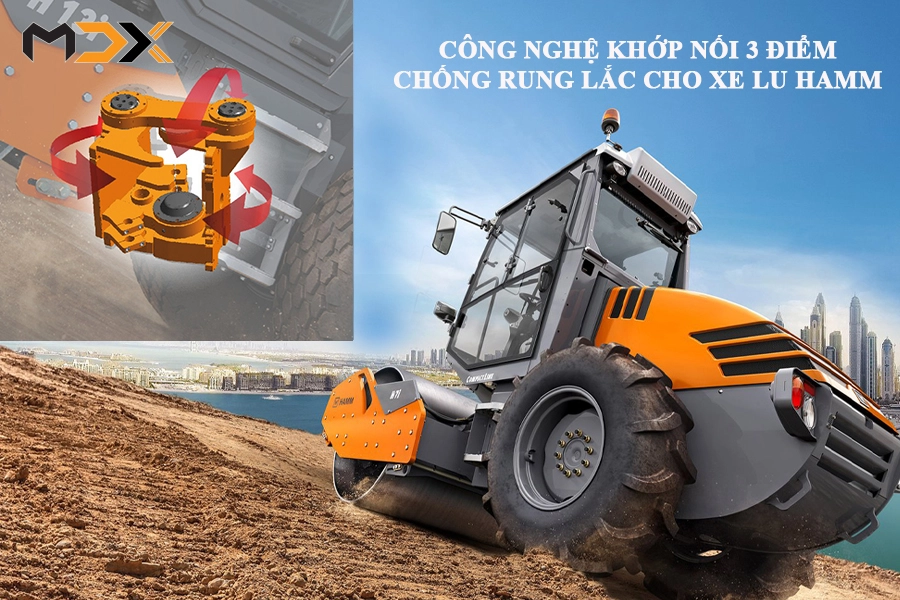
See more at: HERE
HCQ – HAMM COMPACTION QUALITY
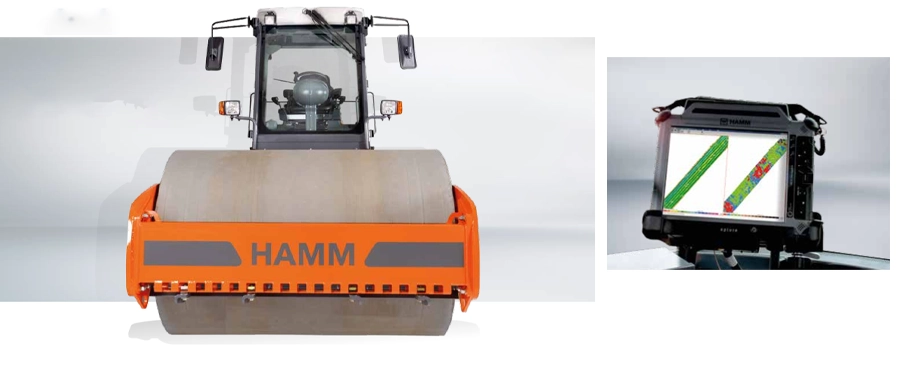
See more at: HERE
The HCQ modules create transparency, increase compaction quality and make for a high level of efficiency.
HCQ: smart system for maximum compaction quality
High-quality compaction means compacting the ground to the required load-bearing capacity – over the entire area and to the required depth. HAMM has developed various measurement systems to check the compaction and bundled them under the name HCQ. These products aid the measurement, documentation and analysis of the compaction processes and offer the maximum possible flexibility, because they are modular in design and perfectly matched to one another.
HAMM Compaction Meter: measuring subsoil rigidity in real time
The HAMM Compaction Meter (HCM) serves to measure and display the subsoil rigidity. To do so, an acceleration sensor on the drum measures the ground rigidity during dynamic compaction. The measurement result, the HMV value, shows the driver whether or not the subsoil is sufficiently compacted. In many cases, this information helps to reduce the number of passes and avoid over-compaction.
HCQ Navigator: area-wide, homogenous compaction
The HCQ Navigator is a satellite-based documentation system for the collection and display of all important parameters during compaction. It creates a real-time compaction map via the HCQ satellite receiver. It shows the areas that have already been adequately compacted and those that require further compaction on a panel PC in the roller. The data from a number of rollers may also be linked via a WLAN. This enables the roller drivers to compact even more efficiently.
The HCQ Navigator’s mobile panel PC for the display and storage of all measurement data.
HAMMTRONIC (3516 HT, HT P, HT VIO)
The Hammtronic electronic machine management system supports the operator in order to achieve optimum compaction without compromising on safety, cost-efficiency and fuel savings.
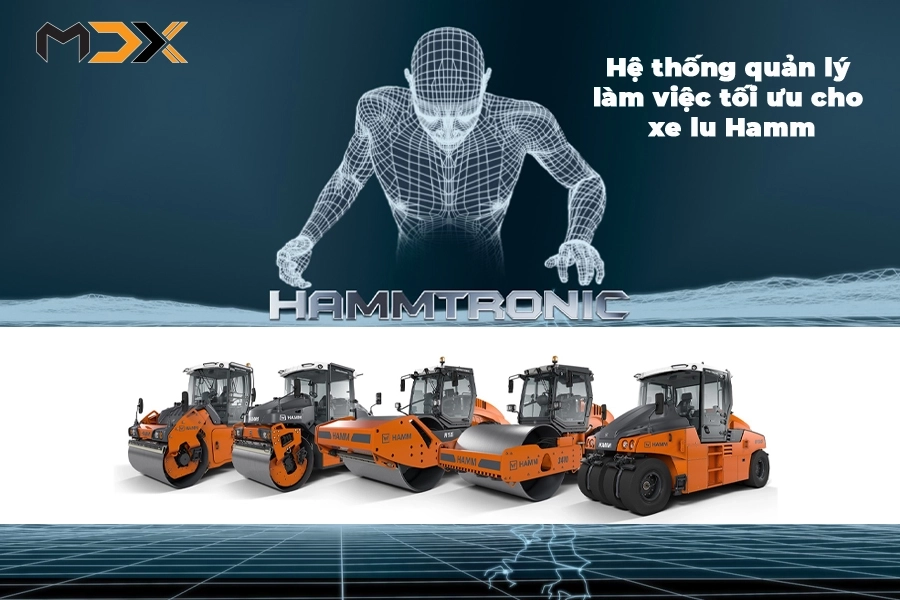
See more at: HERE