WHAT IS FOAMED BITUMEN?
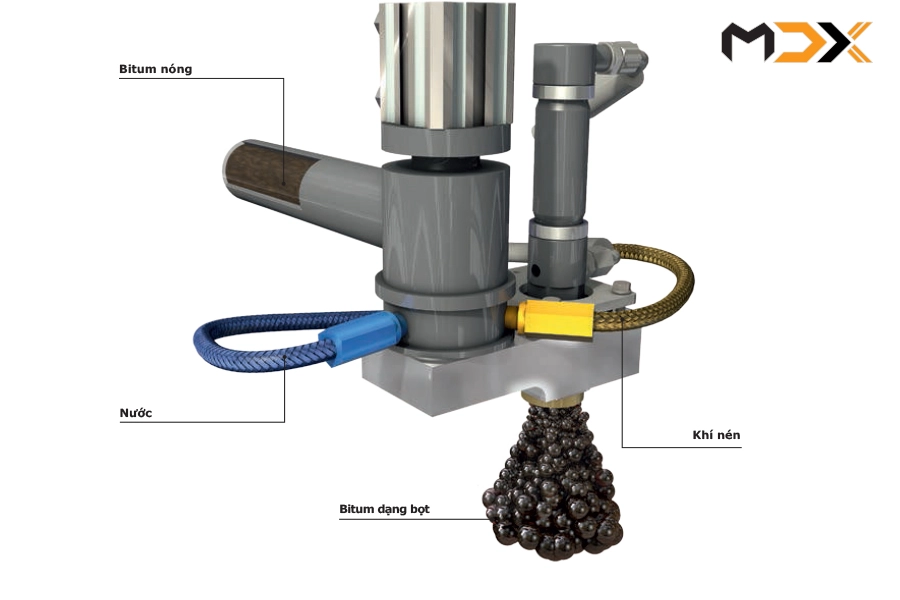
The foamed bitumen injected via the nozzle at the expansion chamber is suitable for direct mixing with the mineral aggregate mixture.
Foamed bitumen is produced from standard grade bitumen used in asphalt road construction. When heated and foamed, bitumen permits the economical production of high-quality base layers. Foamed bitumen is produced by injecting small quantities of water and compressed air into hot bitumen.
The water evaporates, causing the bitumen to foam abruptly and expand to around 15 to 20 times its original volume. The quality of foamed bitumen is primarily described in terms of its expansion ratio and half-life. The larger its expansion and the higher its half-life, the better suited to processing the foamed bitumen will be
Compared to other binders, foamed bitumen offers the advantage of reduced transport and material costs. Bitumen used for the production of foamed bitumen is readily available in all parts of the world.
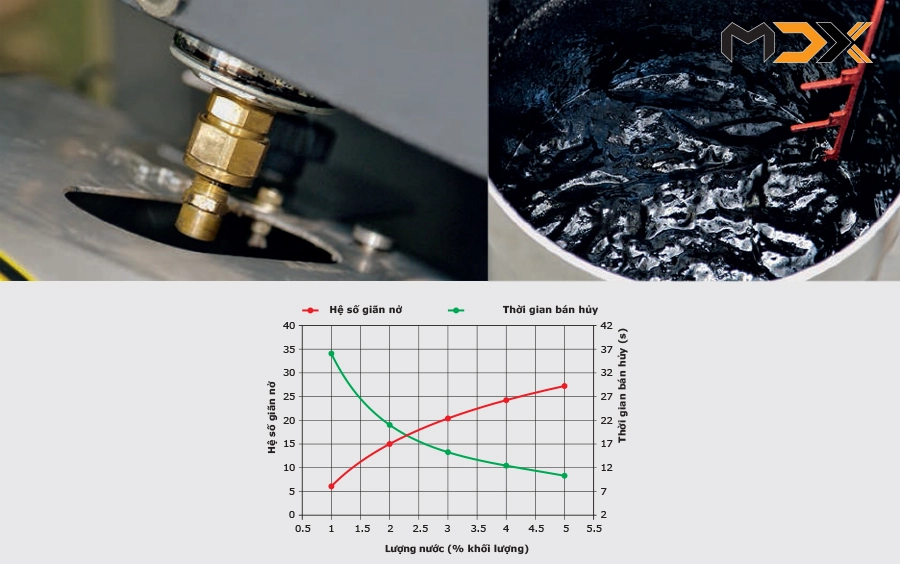
Foaming takes place in expansion chambers where water and air are injected into hot bitumen (160°C to 180°C) at a pressure of approx. 5 bar. Development of half-life and expansion ratio to determine the water
content.
HIGHLIGHTS
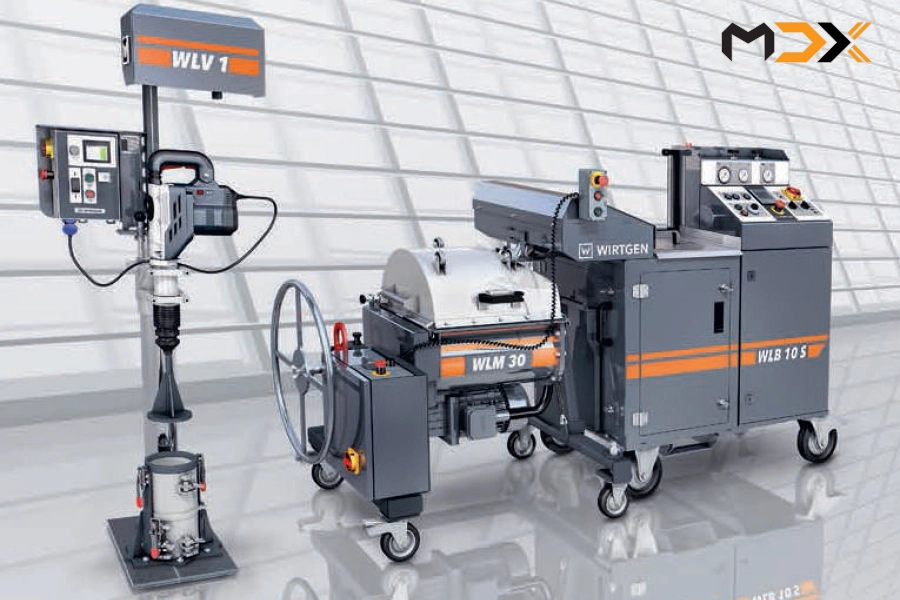
1. WIRTGEN WLV 1 laboratory compactor - 2. WIRTGEN WLM 30 laboratory mixer - 2. WIRTGEN WLB 10 S laboratory foamed bitumen plant
WLB 10 S - SIMULATING THE COLD RECYCLING PROCESS IN THE LABORATORY
WLB 10 S determines the optimum bitumen foam. Foamed bitumen is used to an ever-increasing extent as an economical binder in cold recycling. Preliminary testing with the mobile WLB 10 S laboratory plant enables the foamed bitumen quality to be precisely defined in the laboratory prior to the start of construction. Exceptional ease of operation enables parameters such as water amount, pressure and temperature to be varied quickly and different types of foamed bitumen to be produced within a short time. Based on the results achieved, the WLM 30 laboratory mixer can then be used to determine the composition of the recycling mix.
The plant offers ease of operation and maintenance, as well as a compact, mobile design. It can also be used to test the suitability of mixes with added cement or lime in combination with foamed bitumen.
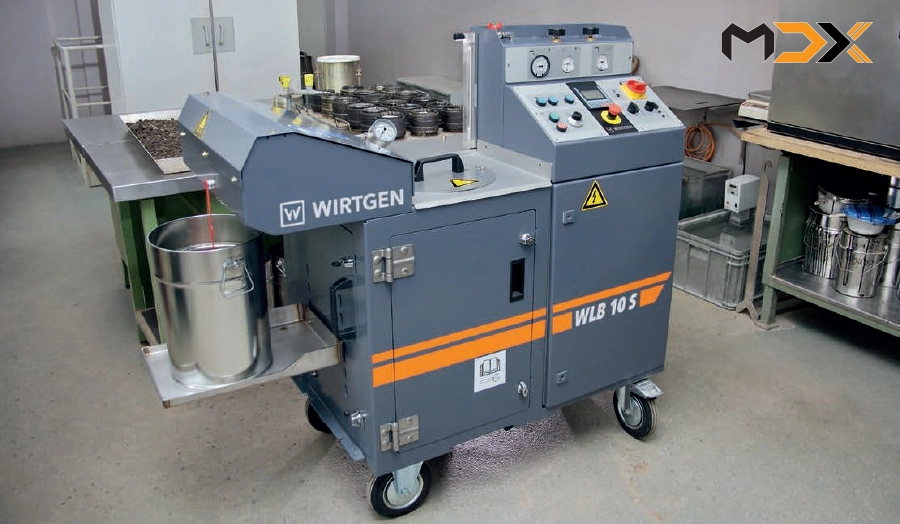
- The compact plant ensures ergonomically optimized handling and ease of operation.
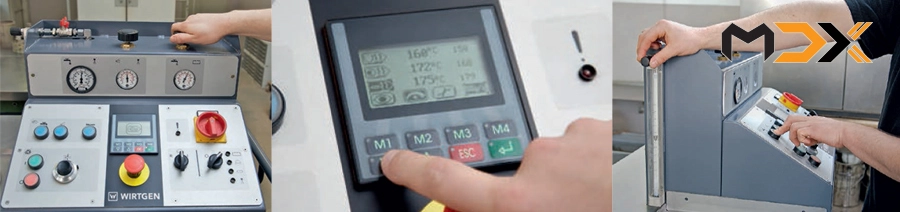
- The clearly and logically structured control panel permits easy setting and monitoring of important parameters.
- Electric control: the plant offers maximum accuracy as it enables calibration of the bitumen flow
- Precise process water settings enable determination of the ideal foamed bitumen quality
WLM 1 - THE IDEAL CHOICE FOR BITUMENSTABILIZED MATERIAL
WLV 1 laboratory compactor for specimen manufacture. The WLV 1 is used for the manufacture of test specimens from bitumen-stabilized material. It is equipped with a powerful vibrating hammer and heavy-duty tamping foot. The efficient path-controlled and time-controlled compaction process is documented via a colour screen. Intuitive operation enables easy adjustment of the specimen height, number of layers and maximum time of compaction.
Compacting multiple layers of equal thickness in a series of specimens achieves consistent compaction results. A standard procedure for the manufacture of test specimens using the WLV 1 has already proven its worth in the industry.
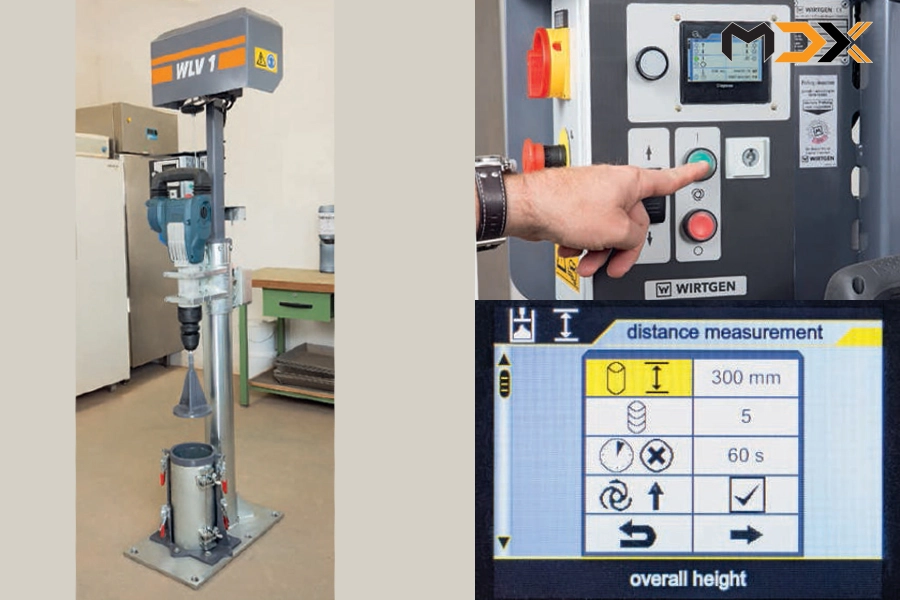
Clearly structured operating concept and simple variation of parameters.
Reliable compaction process
The WLV 1 laboratory compactor offers an ideal solution for the manufacture of specimens from bitumen-stabilized material (BSM).
The core element of the WLV 1 laboratory compactor, a height-adjustable vibrating hammer, is mounted at a vertical column. The vibrating hammer uses a heavy-duty tamping foot to transfer a precisely defined amount of impact energy on the material filled into a cylindrical mould in multiple layers. In the process, a surface roughener is used to ensure a firm bond with the next, upper layer.
Following completion of each compaction process, the vibrating hammer returns to its initial position automatically. This feature substantially increases productivity in the manufacture of test specimens.
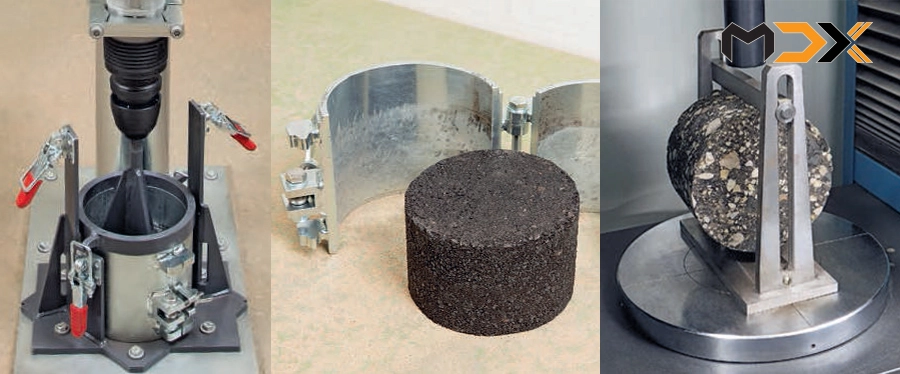
- Specimens of different height are manufactured depending on the testing method.
- Quality check by performing the indirect tensile strength test.
Perfect specimens for different testing methods
Once the specified final height of the specimen has been achieved, the specimen can simply be removed from the mould by means of a quick-release fastener and then prepared for the testing method to be applied.
Specimens of 152 mm in diameter and 95 mm in height can be produced to determine the indirect tensile strength (ITS).
Large specimens of 152 mm in diameter and 300 mm in height are produced for use in triaxial testing.
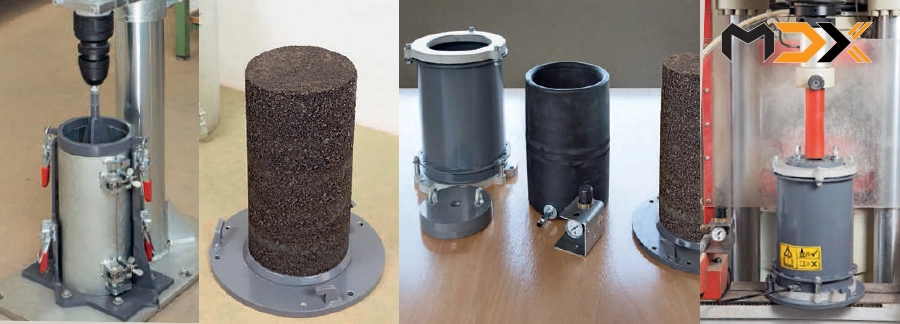
- Even large specimens can be manufactured quite easily.
- WIRTGEN also supplies triaxial testing equipment.
WLM 30 - MIXES EVERY BIT AS HOMOGENEOUS AS ON THE CONSTRUCTION SITE
Direct injection of the foamed bitumen into the mixing chamber of the WLM 30 laboratory mixer enables mixes to be processed under real-life conditions and test specimens to be manufactured. In addition, the twin-shaft compulsory mixer is perfectly matched to the aboratory plant in terms of design and performance.
The high mixing intensity corresponds to that of continuous mixers used on the construction site. The WLM 30 has a filling capacity of approx. 30 kg and offers variable settings for speed and mixing time. The mixing chamber is simply pivoted downwards about 180° and the cover opened to allow discharge of the mix. And what’s more: when used separately, the WLM 30 is suitable for the production of a wide variety of mix compositions.
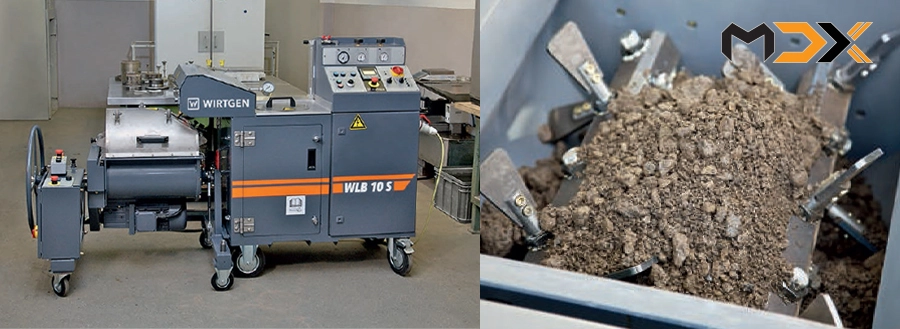
The powerful mixer with heavy-duty mixing blades produces a wide variety of cold mixes
MORE CONTROL - IMPROVED QUALITY.
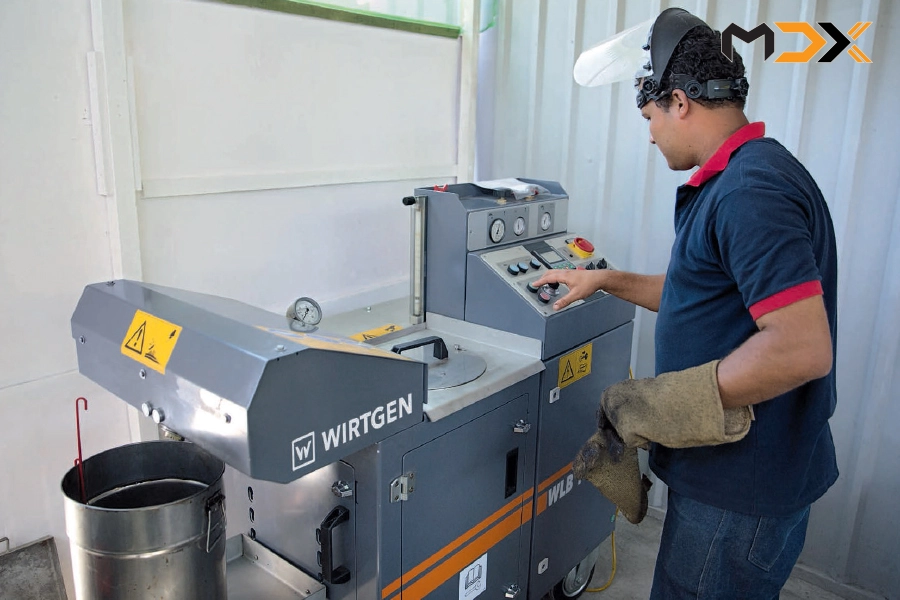
The laboratory foamed bitumen plant performs a series of precise measurements to determine the optimum foamed bitumen properties.
The different parameters can be varied quite easily during the process.
The most suitable composition of the recycling mix is determined quickly in combination with the laboratory mixer.
The mix can then be used to manufacture test specimens using the laboratory compactor.
The high-quality machines are perfectly tailored for use in cold recycling and comply with the high quality standards set by testing laboratories.
MOBILE DESIGN
Mobile concept: The foamed bitumen plant and laboratory mixer are mounted on wheels to allow easy repositioning.
Compact machine dimensions: compact machines to allow flexible handling in the laboratory.
Integrated air compressor: optional air compressor to allow operation without an external compressed air supply.
SIMPLE, INTUITIVE OPERATING CONCEPT
Ergonomic design: ergonomically designed controls for intuitive operation.
Clarity: clearly and logically structured control panels for straightforward, intuitive operation.
Simple variation of parameters WLB 10 S: quick and highly precise variation of parameters to produce the best foamed bitumen quality within a short period of time.
PRODUCING FOAMED BITUMEN OF HIGH QUALITY
High-quality bitumen injection nozzle: special, high-precision bitumen injection nozzle with expansion chamber to ensure optimum bitumen foaming behaviour.
Fully heated bitumen system: All components transporting bitumen are heated to ensure reliable sample production.
Highest metering accuracy: calibrated bitumen flow and precise process water settings to determine the optimum foamed bitumen quality
PERFECT MIXES
High mixing intensity: powerful twin-shaft compulsory mixer with mixing blades manufactured from highly wear-resistant material for optimum, real-life mixing results.
Variable speed settings: continuously adjustable mixing speed and separately adjustable mixing time.
Broader range of applications: the laboratory mixer can be used independently to produce a wide range of different mix compositions.
Perfectly matched machinery: laboratory mixer and foamed bitumen plant can be connected quite easily to allow direct discharge of the bitumen foam into the mixer.
EFFICIENT MANUFACTURE OF TEST SPECIMENS
Extremely simple, tried-and-tested process: Compactor including vibrating hammer for the manufacture of test specimens.
Defined impact energy: Powerful vibrating hammer with heavy-duty tamping foot.
Optimum compaction: Effortless monitoring of the path-controlled and time-controlled compaction process.
Standardized process: Tried-and-tested method in the industry
TECHNICAL DATA
Dimensions (L x W x H) |
1 450 x 685 x 1 345 mm |
Bitumen pump |
electrically heated gear pump |
Bitumen temperature |
140 - 200 °C |
Water content |
0 - 5 % of bitum |
Air pressure |
0 - 10 bar |
Electrical system |
suitable for different mains power systems |
Own weight |
270 kg |